By using state-of-the-art European imported machineries, we ensure our production capacity and are able to manufacture and ship up to 35 containers per month. Our production process adheres to the highest standards, incorporating advanced CNC systems to guarantee consistency and excellence.
PANEL & VENEER TRANSFORMATION
Our Panel & Veneer department focuses on transforming MDF panels and selecting veneers to create exceptional finishes. We work closely with our clients to choose the perfect veneer, ensuring the most desirable outcome for their furniture designs.
SAWMILL & WOOD DRYING
During this process, logs are cut into lumber and kiln dried to reduce their moisture content. These preliminary steps are extremely important for producing long-lasting furniture. Therefore, we pay great attention to these processes and only use specialised equipment to ensure a quality result.
SOLID WOOD TRANSFORMATION
Our solid wood department is focused on producing high-quality components. We ensure that every component meets the highest standards of quality and precision.
METAL TRANSFORMATION
Our metal division is fully equipped and has experienced significant growth over the past years. With capabilities ranging from precision laser cutting to durable powder coating, we offer a complete range of services to manufacture products tailored to our client's needs.
MINERAL COATING
We have been working with mineral coatings since 2015, continuously evolving and learning new techniques to enhance our offerings. Our expertise allows us to propose various types of textures and finishes.
SANDING & FINISHING
Finishing is a crucial step in achieving the desired quality of the final product. We apply the perfect finishing touches that bring out the natural beauty of the wood or veneer. Our attention to detail in this final step guarantees a product that is not only visually stunning but also built to last.
By using state-of-the-art European imported machineries, we ensure our production capacity and are able to manufacture and ship up to 35 containers per month. Our production process adheres to the highest standards, incorporating advanced CNC systems to guarantee consistency and excellence.
PANEL & VENEER TRANSFORMATION
Our Panel & Veneer department focuses on transforming MDF panels and selecting veneers to create exceptional finishes. We work closely with our clients to choose the perfect veneer, ensuring the most desirable outcome for their furniture designs.
SAWMILL & WOOD DRYING
During this process, logs are cut into lumber and kiln dried to reduce their moisture content. These preliminary steps are extremely important for producing long-lasting furniture. Therefore, we pay great attention to these processes and only use specialised equipment to ensure a quality result.
SOLID WOOD TRANSFORMATION
Our solid wood department is focused on producing high-quality components. We ensure that every component meets the highest standards of quality and precision.
METAL TRANSFORMATION
Our metal division is fully equipped and has experienced significant growth over the past years. With capabilities ranging from precision laser cutting to durable powder coating, we offer a complete range of services to manufacture products tailored to our client's needs.
MINERAL COATING
We have been working with mineral coatings since 2015, continuously evolving and learning new techniques to enhance our offerings. Our expertise allows us to propose various types of textures and finishes.
SANDING & FINISHING
Finishing is a crucial step in achieving the desired quality of the final product. We apply the perfect finishing touches that bring out the natural beauty of the wood or veneer. Our attention to detail in this final step guarantees a product that is not only visually stunning but also built to last.
ASSEMBLING & QC INSPECTION
In the assembling phase, our team brings together each component with precision and expertise. Every part is aligned and fastened to ensure structural integrity. Following assembly, each product undergoes a complete quality control inspection. Every detail is examined, from the functionality and durability of moving parts to the finish and visual appeal.
PACKING
Packing is more than just a final step - it’s a critical part of ensuring the safe arrival of our products. We carefully prepare each item, using tailored packaging solutions designed to provide maximum protection during transport.
Turning concept into creation : Your design, Our Expertise
Our Research and Development team is dedicated to bringing your dream design to life. By closely collaborating with you, we ensure that each concept is adapted to seamlessly align with our production capabilities. From the initial sketches to the final product, we focus on every detail, balancing innovation with practicality. Let us transform your vision into a beautifully crafted reality
Our expertise and machinery gives us flexibility, precision, and quality, but excellent machining capabilities would mean little without a reliable supply of materials.
Our VENEER selection is carefully curated for quality and includes primarily Oak, Walnut, and Teak. Our Teak originates from Javanese government-managed plantations and is SVLK certified, while our Oak is imported from Europe and sourced from PEFC-certified forests and suppliers.
Since 2015, we have specialised in MINERAL COATING, continuously refining our techniques to expand our expertise. We offer a range of tailored finishes and colours.
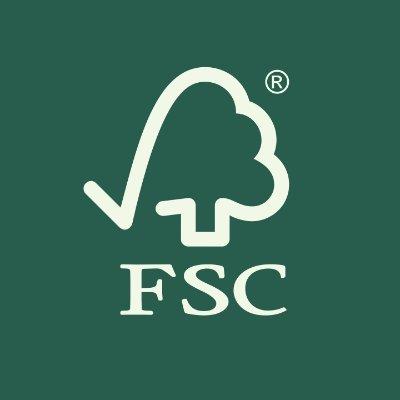
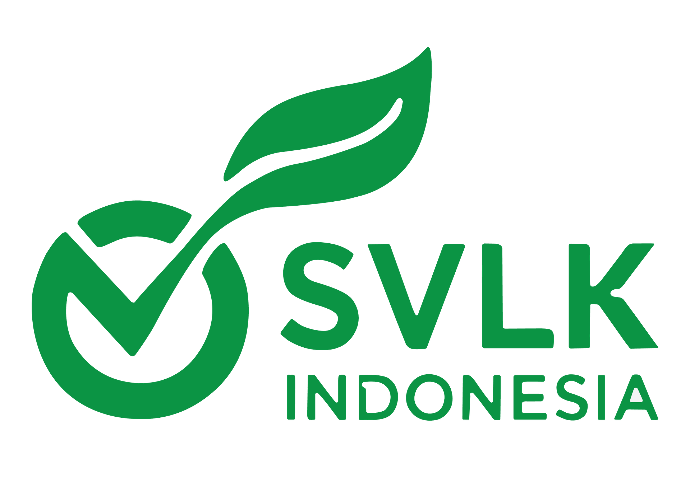
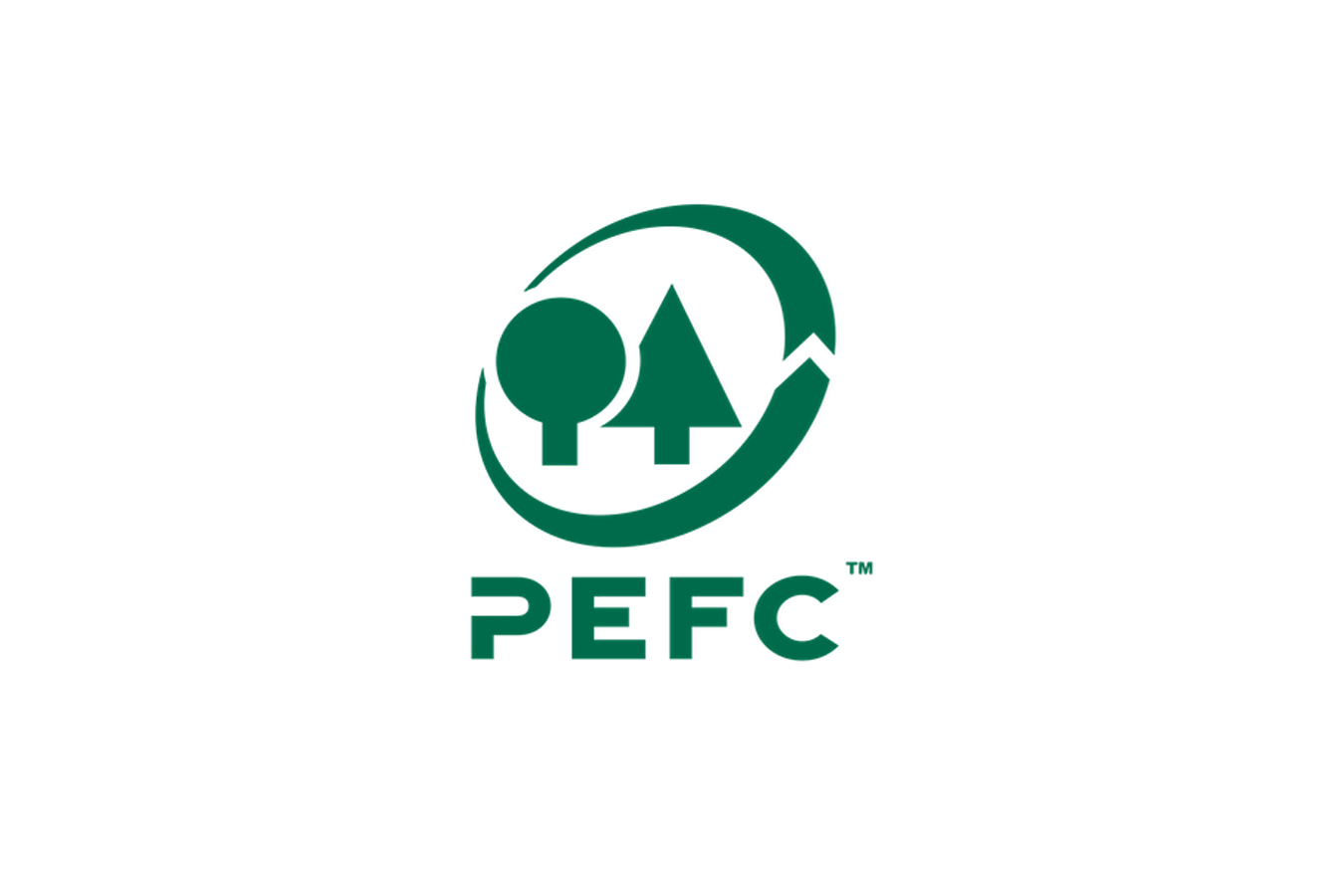
Our solid METAL and iron plates or pipes are sourced from trusted suppliers such as BLUM, HETTICH, HAFELE, CAMAR, POËTKER, and DTC. We offer a great variety of sizes.
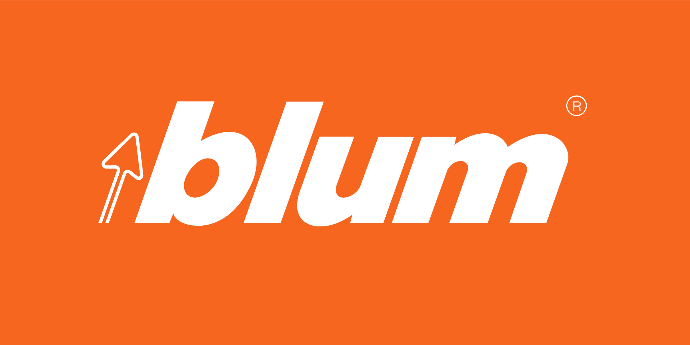

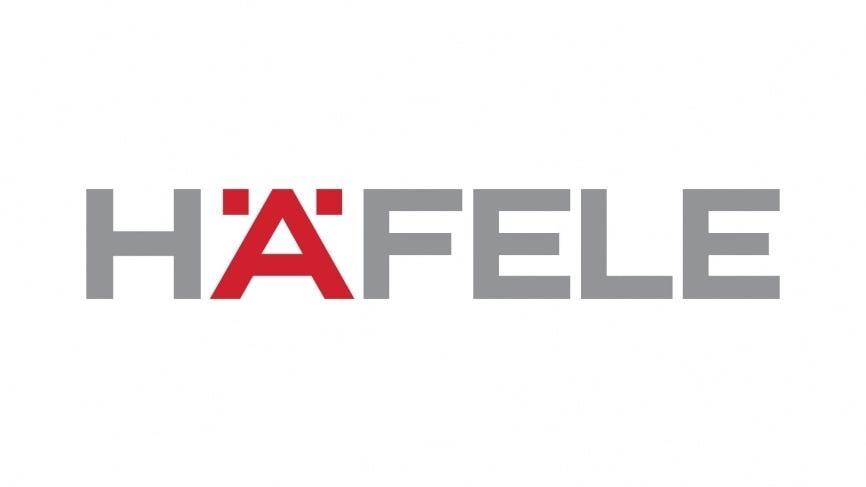
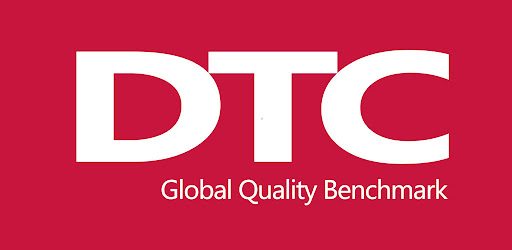
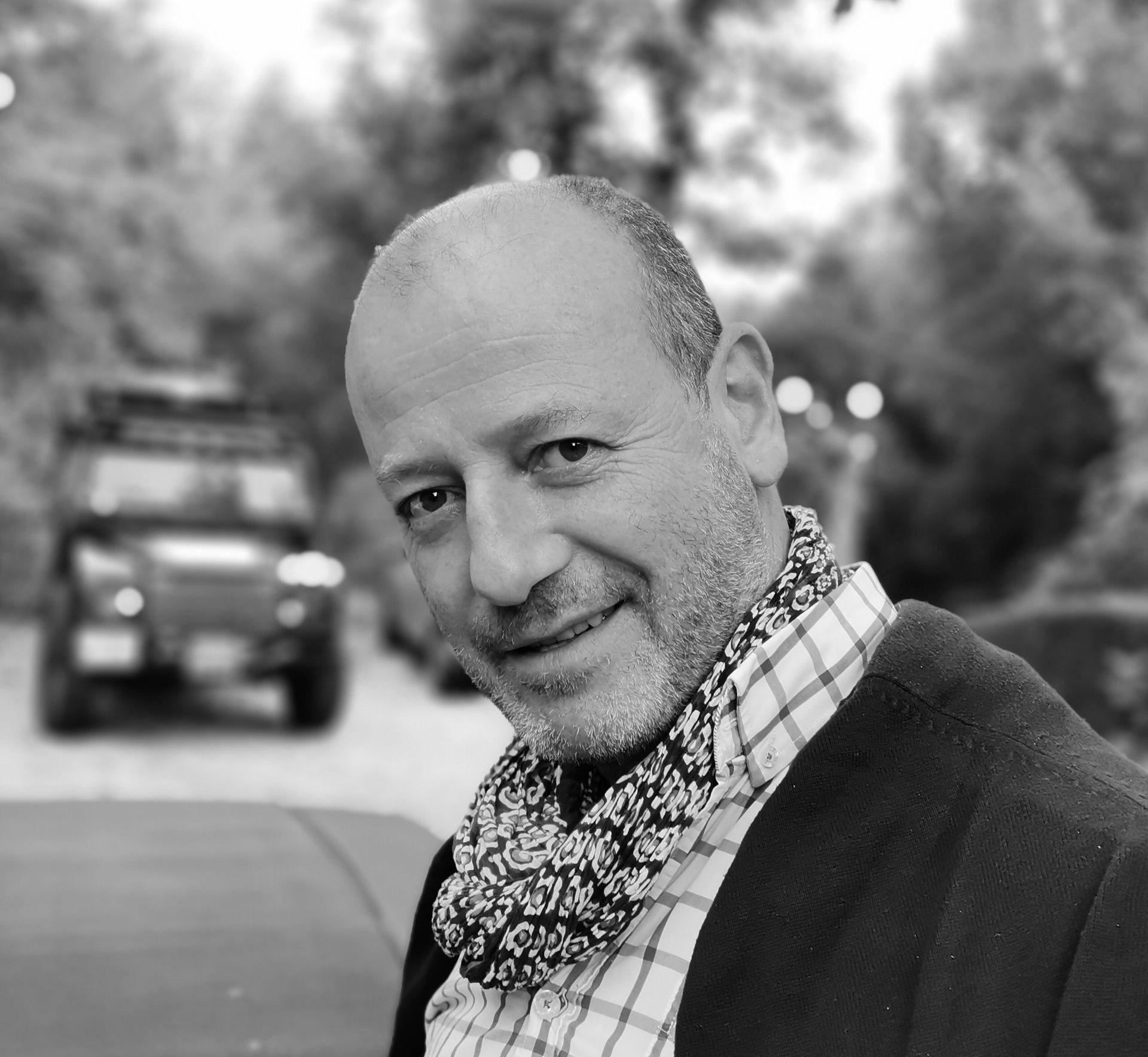
Cédric Levie, CEO
PT. MAXIM INDOWOOD was founded in 1998 by Cédric Levie, a visionary entrepreneur from Belgium. Starting from humble beginnings, the factory quickly grew under Cédric’s guidance. His dedication to quality, sustainability, and innovation helped transform the business from a small workshop into a state-of-the-art production facility. Today, the company spans over 25,000 square meters and is fully mechanised, a testament to the harmonious integration of modern technology. With a workforce of over 500 people, PT. MAXIM INDOWOOD is committed not only to excellence in production but also to creating a positive impact on the local community by providing sustainable employment and skill development.
FAQ
Our MOQ is 10 pieces per item, and orders must be configured to fit into 20FT, 40FT, or 40HC containers.
Our minimum lead time is 12 weeks from the receipt of the deposit (30% of the order) and the Estimated Time of Departure (ETD).
The lead time may also depend on our production schedule and the complexity of the order.
Our prices include standard packaging with black printed shipping marks. Upgrades in packaging and/or shipping marks are subject to additional fees.
Our prices are FOB Semarang.
To confirm an order, a 30% deposit is required. The remaining 70% will be invoiced once the order departs from our factory.
Legal documents will be provided after full payment is received.
We currently do not have a catalog, as we mainly produce designs based on our customers' ideas.
Jl. Jend. Soejarwo, RT 13/RW04
Desa Bandengan, Jepara JT 59432, Indonesia
Opening Hours
Monday to Friday 07:30 - 16:30
By using state-of-the-art European imported machineries, we ensure our production capacity and are able to manufacture and ship up to 35 containers per month. Our production process adheres to the highest standards, incorporating advanced CNC systems to guarantee consistency and excellence.
Our Panel & Veneer department focuses on transforming MDF panels and selecting veneers to create exceptional finishes. We work closely with our clients to choose the perfect veneer, ensuring the most desirable outcome for their furniture designs.
ASSEMBLING & QC INSPECTION
In the assembling phase, our team brings together each component with precision and expertise. Every part is aligned and fastened to ensure structural integrity. Following assembly, each product undergoes a complete quality control inspection. Every detail is examined, from the functionality and durability of moving parts to the finish and visual appeal.
PACKING
Packing is more than just a final step - it’s a critical part of ensuring the safe arrival of our products. We carefully prepare each item, using tailored packaging solutions designed to provide maximum protection during transport.
Turning concept into creation : Your design, Our Expertise
Our Research and Development team is dedicated to bringing your dream design to life. By closely collaborating with you, we ensure that each concept is adapted to seamlessly align with our production capabilities. From the initial sketches to the final product, we focus on every detail, balancing innovation with practicality. Let us transform your vision into a beautifully crafted reality.
Our expertise and machinery gives us flexibility, precision, and quality, but excellent machining capabilities would mean little without a reliable supply of materials.
Our VENEER selection is carefully curated for quality and includes primarily Oak, Walnut, and Teak. Our Teak originates from Javanese government-managed plantations and is SVLK certified, while our Oak is imported from Europe and sourced from PEFC-certified forests and suppliers.
Since 2015, we have specialised in MINERAL COATING, continuously refining our techniques to expand our expertise. We offer a range of tailored finishes and colours.
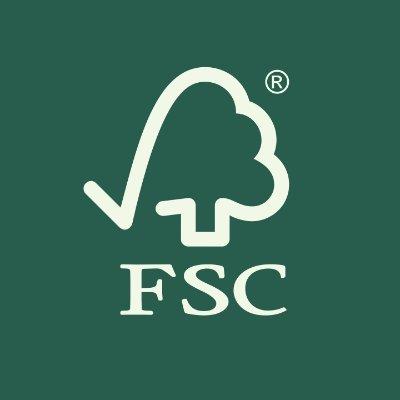
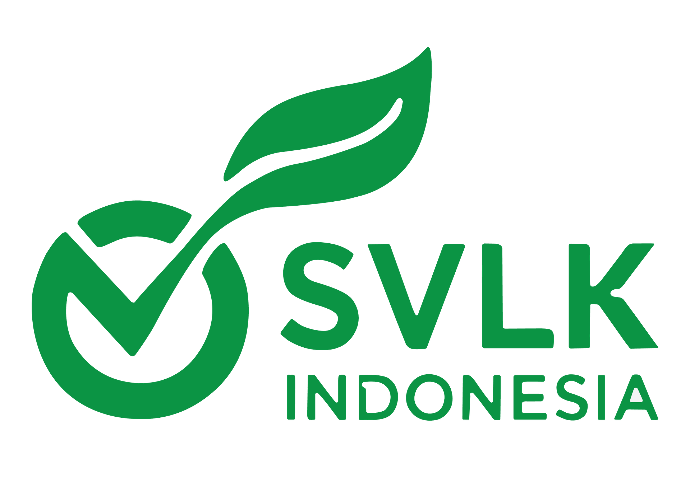
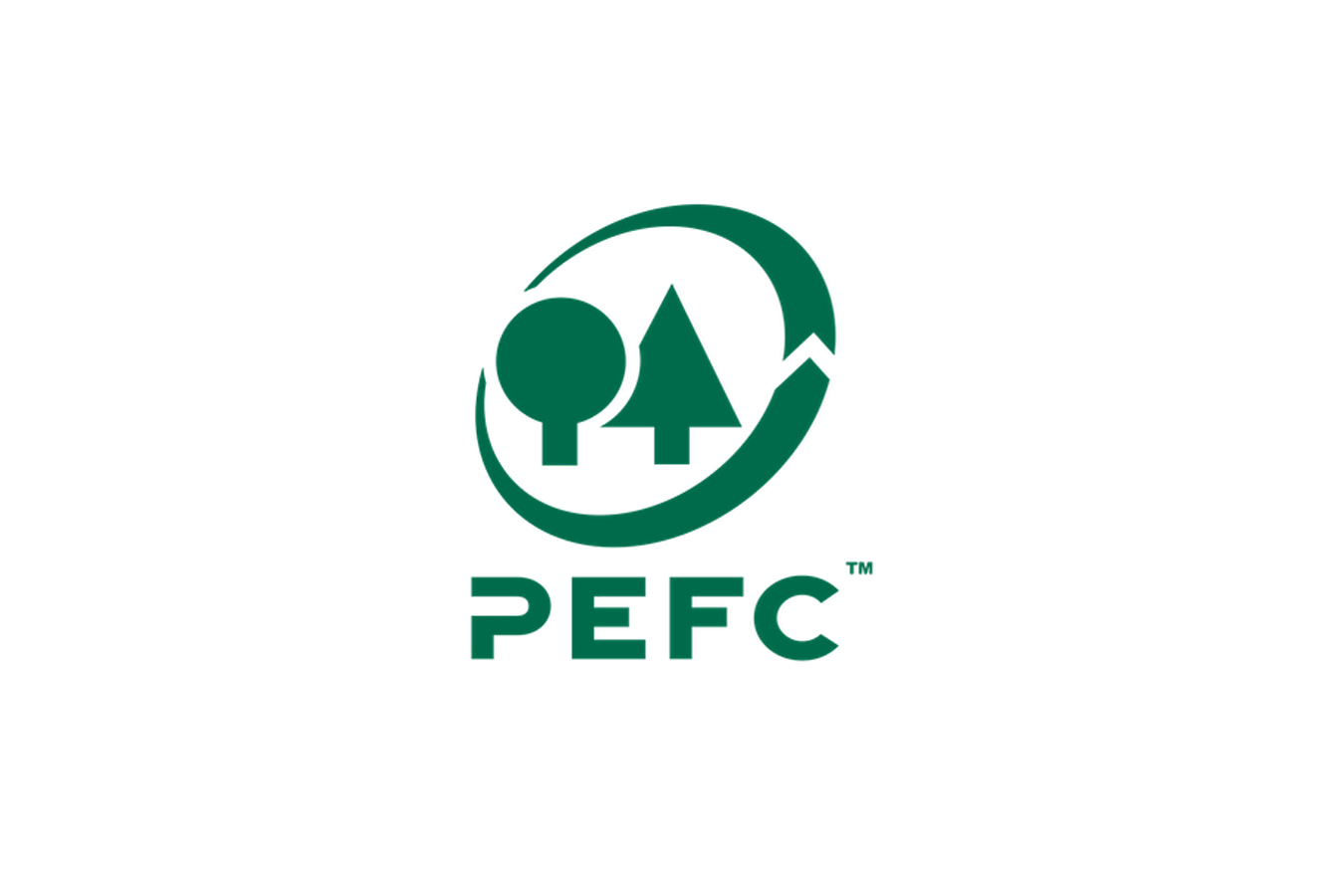
Our solid METAL and iron plates or pipes are sourced from trusted suppliers such as BLUM, HETTICH, HAFELE, CAMAR, POËTKER, and DTC. We offer a great variety of sizes.
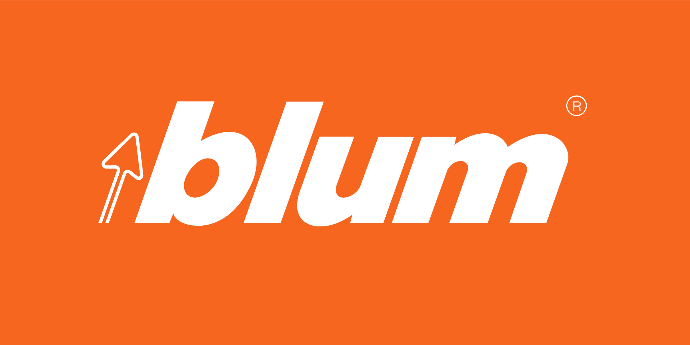

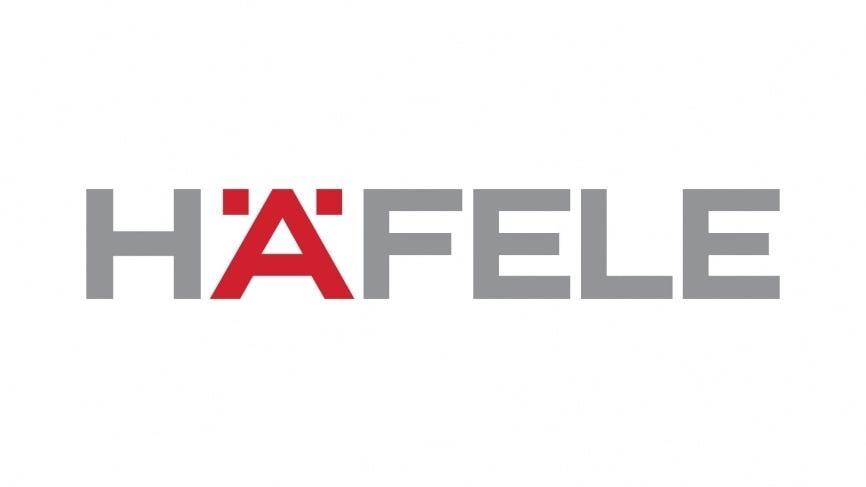
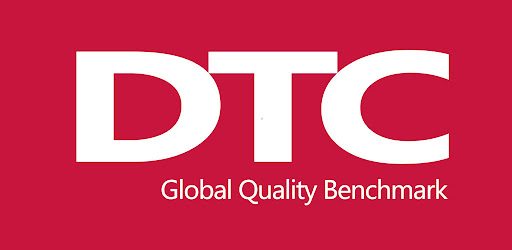
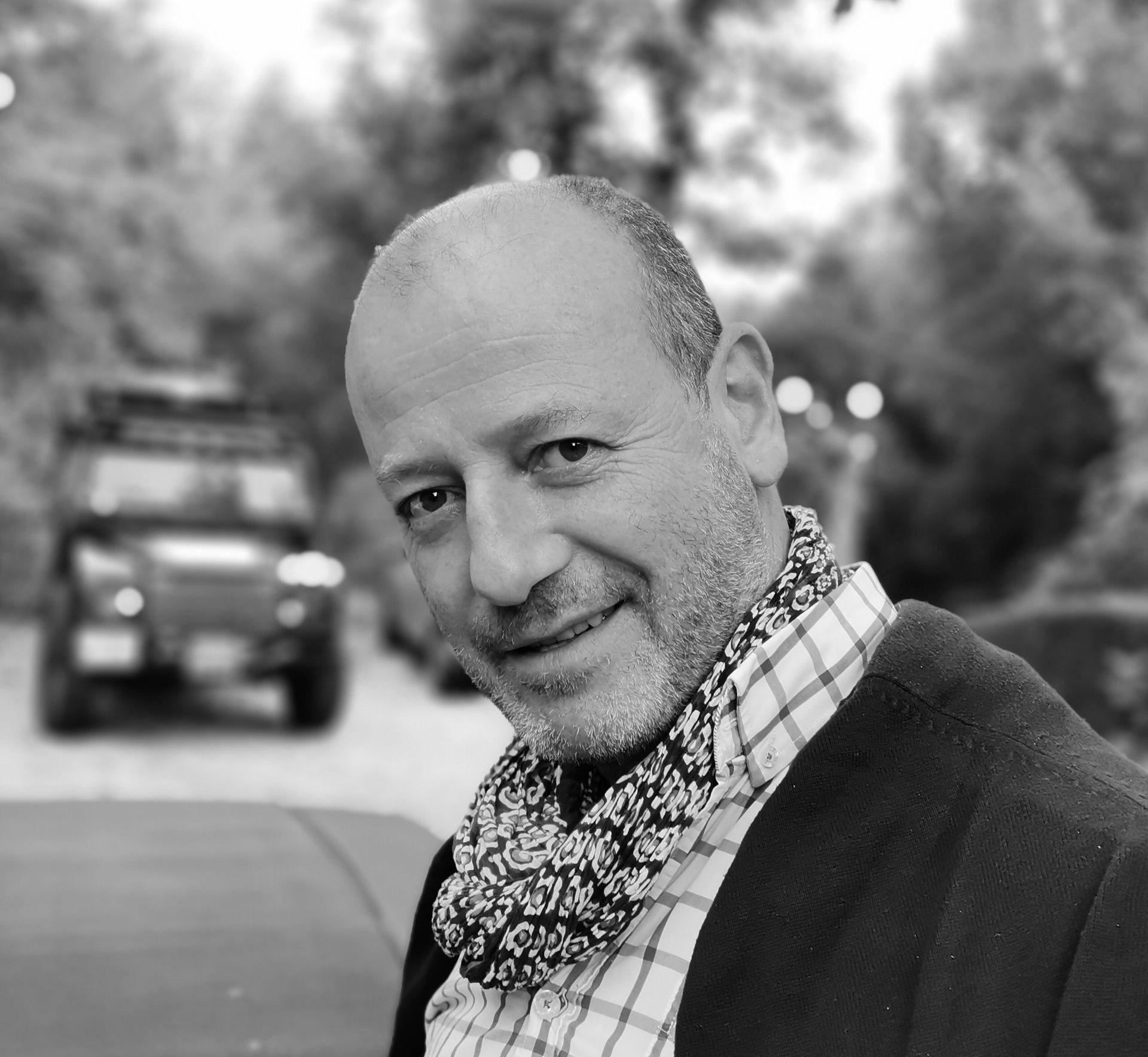
Cédric Levie, CEO
PT. MAXIM INDOWOOD was founded in 1998 by Cédric Levie, a visionary entrepreneur from Belgium. Starting from humble beginnings, the factory quickly grew under Cédric’s guidance. His dedication to quality, sustainability, and innovation helped transform the business from a small workshop into a state-of-the-art production facility. Today, the company spans over 25,000 square meters and is fully mechanised, a testament to the harmonious integration of modern technology. With a workforce of over 500 people, PT. MAXIM INDOWOOD is committed not only to excellence in production but also to creating a positive impact on the local community by providing sustainable employment and skill development.
FAQ
Our MOQ is 10 pieces per item, and orders must be configured to fit into 20FT, 40FT, or 40HC containers.
Our minimum lead time is 12 weeks from the receipt of the deposit (30% of the order) and the Estimated Time of Departure (ETD).
The lead time may also depend on our production schedule and the complexity of the order.
Our prices include standard packaging with black printed shipping marks. Upgrades in packaging and/or shipping marks are subject to additional fees.
Our prices are FOB Semarang.
To confirm an order, a 30% deposit is required. The remaining 70% will be invoiced once the order departs from our factory.
Legal documents will be provided after full payment is received.
We currently do not have a catalog, as we mainly produce designs based on our customers' ideas.
Jl. Jend. Soejarwo, RT 13/RW04
Desa Bandengan, Jepara JT 59432, Indonesia
Opening Hours
Monday to Friday 07:30 - 16:30
During this process, logs are cut into lumber and kiln dried to reduce their moisture content. These preliminary steps are extremely important for producing long-lasting furniture. Therefore, we pay great attention to these processes and only use specialised equipment to ensure a quality result.
Our solid wood department is focused on producing high-quality components. We ensure that every component meets the highest standards of quality and precision.
Our metal division is fully equipped and has experienced significant growth over the past years. With capabilities ranging from precision laser cutting to durable powder coating, we offer a complete range of services to manufacture products tailored to our client's needs.
We have been working with mineral coatings since 2015, continuously evolving and learning new techniques to enhance our offerings. Our expertise allows us to propose various types of textures and finishes.
Finishing is a crucial step in achieving the desired quality of the final product. We apply the perfect finishing touches that bring out the natural beauty of the wood or veneer. Our attention to detail in this final step guarantees a product that is not only visually stunning but also built to last.
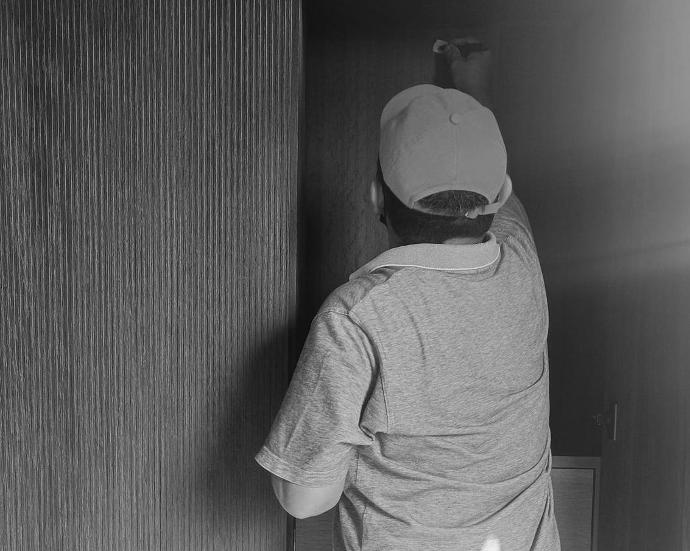
In the assembling phase, our team brings together each component with precision and expertise. Every part is aligned and fastened to ensure structural integrity. Following assembly, each product undergoes a complete quality control inspection. Every detail is examined, from the functionality and durability of moving parts to the finish and visual appeal.
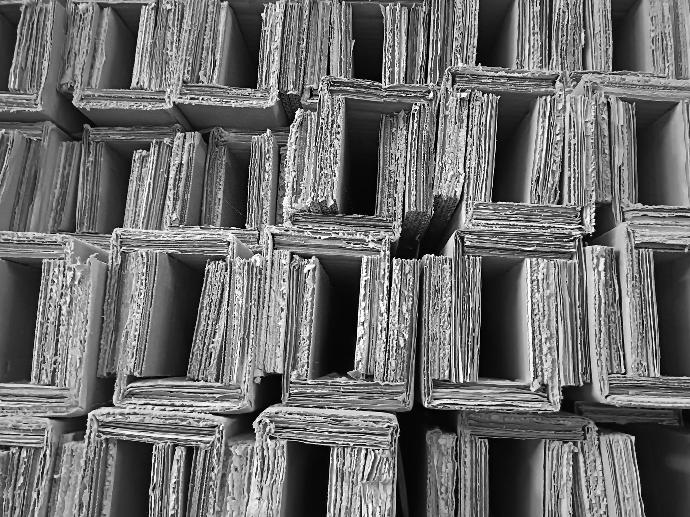
Packing is more than just a final step - it’s a critical part of ensuring the safe arrival of our products. We carefully prepare each item, using tailored packaging solutions designed to provide maximum protection during transport.
Turning concept into creation
Your design, Our Expertise
Our Research and Development team is dedicated to bringing your dream design to life. By closely collaborating with you, we ensure that each concept is adapted to seamlessly align with our production capabilities. From the initial sketches to the final product, we focus on every detail, balancing innovation with practicality. Let us transform your vision into a beautifully crafted reality.
Our expertise and machinery gives us flexibility, precision, and quality, but excellent machining capabilities would mean little without a reliable supply of materials.
Our VENEER selection is carefully curated for quality and includes primarily Oak, Walnut, and Teak. Our Teak originates from Javanese government-managed plantations and is SVLK certified, while our Oak is imported from Europe and sourced from PEFC-certified forests and suppliers.
Since 2015, we have specialised in MINERAL COATING, continuously refining our techniques to expand our expertise. We offer a range of tailored finishes and colours.
Our solid METAL and iron plates or pipes are sourced from trusted suppliers such as BLUM, HETTICH, HAFELE, CAMAR, POËTKER, and DTC. We offer a great variety of sizes.
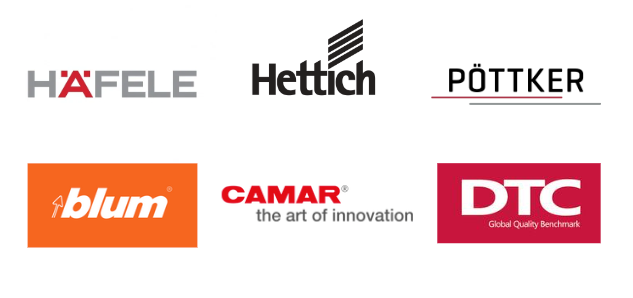
FAQ
Our MOQ is 10 pieces per item, and orders must be configured to fit into 20FT, 40FT, or 40HC containers.
Our minimum lead time is 12 weeks from the receipt of the deposit (30% of the order) and the Estimated Time of Departure (ETD). The lead time may also depend on our production schedule and the complexity of the order.
Our prices include standard packaging with black printed shipping marks. Upgrades in packaging and/or shipping marks are subject to additional fees. Our prices are FOB Semarang.
To confirm an order, a 30% deposit is required. The remaining 70% will be invoiced once the order departs from our factory. Legal documents will be provided after full payment is received.
We currently do not have a catalog, as we mainly produce designs based on our customers' ideas.